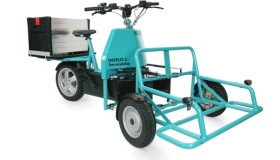
INVENT Press Release
The latest new addition to our range of mixing and aeration systems are the service e-bikes for high load capacities. What at first may seem surprising does in fact make sense upon closer look.
From courier and delivery services to transport services for small goods, more and more companies are relying on e-bikes and cargo bikes. Even our CEO Dr. Marcus Höfken is expressing his enthusiasm about the development in this direction. He has always had an interest in vehicles of any kind, and so in his mind, the idea developed to include in the product range a suitable service e-bike for INVENT customers.
The INVELO:3 service e-bike comes with those essential features that INVENT products are known for: high quality, reliable functionality and energy efficiency. In addition, the three-wheeled runaround made in Germany also offers a huge scoop of fun. The three-wheeled cargo-mobile, 2.2 m in length and 1 m in width, can be loaded with up to 100 kg on the front wheel and up to 60 kg on the rear wheel.
High-tech vehicles with high-quality components
The alignment of the undercarriage, the design of the braking system and the steering system were developed together with experienced racing engineers from the automotive industry. The result was a safe driving and cornering feel even when fully loaded.
With its high torque and exceptional performance characteristics, there are no compromises when it comes to the design of the powerful mid-engine, which is aligned for the professional use in a service bike. The control system features powerful electronics that are directly incorporated in the drive technology. The three-stage gearbox lets the cyclist’s pedaling frequency and effort be perfectly balanced, without the need for any external gear shifting and the additional maintenance that this would require. The power transmission utilizes a heavy-duty motorcycle chain to guarantee long service life.
What’s more, the INVELO:3 makes no compromises when it comes to safety. The hydraulic 3-disc brake system has been designed to meet the highest demands and ensure a long service life. With its large brake discs and finely adjustable braking effect, it brings the INVELO:3 to a stop quickly and safely, even with a full load.
The powerful, durable battery packs, each with a battery capacity of 1 kWh, are easy to install and remove or charged directly on the INVELO:3. The battery packs can be quickly recharged from a standard 230-volt socket. This allows the service e-bike reach a maximum speed of 25 km/h and a range of approx. 50 km.
The tires feature durable rims especially developed and designed to meet the requirements of tough commercial use. The robust wheel sets used have been tested for maximum loads and durability. Not only are they capable of absorbing maximum lateral forces under load, but their large tire contact area is impressive, featuring maximum running performance and breakdown safety.
All components of the INVELO:3 have been developed and selected for long service-life and durability. To reach the foreseeable and calculable service intervals, the product was designed to ensure that wear parts such as brakes and tires are easy to replace.
Also new: INVELO:4 available in the webshop soon
The compact power packs are ideal for reducing the workload of wastewater treatment plant attendants and maintenance. Especially in large-scale plants, such as those that have to be maintained in major cities around the world, we understand the transport needs of technical staff for tools and materials.
With this high-quality vehicle that is currently offered in our webshop at a price of € 9,975, Marcus Höfken has placed yet another product in the shopping cart for our sales department, which satisfied customers can immediately appreciate and identify with.
The INVELO:3 will soon not be the only service e-bike in the webshop. Its four-wheel “big brother”, INVELO:4, packs even more power onto the road thanks to twice the battery power. Weighing a quarter of a ton, with a payload of 250 kg and a cargo volume of two cubic meters, the stylish vehicle not only boasts measurable added value but, like the INVELO:3, is a real eye-catcher.
Needless to say, the “pack mules” are not only suitable for use in wastewater treatment plants. That’s why we are just as happy to receive orders from other industries and for private use.
By the way: The purchase of the electric service bikes is subsidized by the German Federal Office of Economics and Export Control. The subsidy is 25% of the purchase price, up to a maximum of EUR 2,500. Proof of commercial use is required. The basis is the guideline for the subsidization of e-load bicycles and e-load trailers for bicycle-bound freight transport, published by the Federal Ministry for the Environment, Nature Conservation and Nuclear Safety.